Fastener failure occurs when a mechanical fastener fails to perform its intended function. Fastener failure can lead to serious consequences, such as equipment damage, property damage, and even loss of life. In this article, we will discuss what is fastener failure, the causes of fastener failure, prevention of fastener failure, failure analysis, fastener failure modes, fastener pull through failure, best practices for avoiding fastener failure, testing and inspection methods for fastener failure, and case studies of fastener failure.
Table of Contents
What is Fastener Failure?
Fastener failure occurs when a mechanical fastener fails to perform its intended function. Fasteners are used to join two or more objects together and are an integral part of most engineering and construction projects. Fasteners are designed to hold and transfer loads, but they can fail if they are not designed, installed, or maintained properly. Fastener failure can lead to serious consequences, such as equipment damage, property damage, and even loss of life.
It is important to understand the causes and prevention of fastener failure in order to ensure the safety and reliability of the structure. There are numerous factors that can lead to fastener failure, including improper installation, inadequate tightening, incorrect material selection, incorrect fastener design, corrosion, fatigue, and overloading.
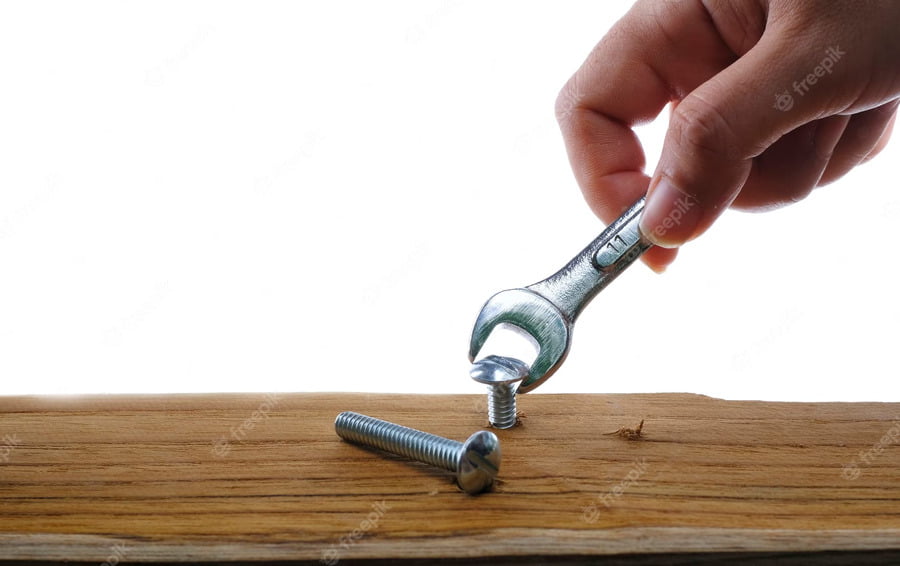
Causes of Fastener Failure
The most common causes of fastener failure are improper installation, inadequate tightening, incorrect material selection, incorrect fastener design, corrosion, fatigue, and overloading. Improper installation is often caused by the use of an incorrect fastener size or the wrong type of fastener for the application. Inadequate tightening can be caused by the use of improper tools or techniques. Incorrect material selection can lead to premature failure due to corrosion and fatigue. Incorrect fastener design can cause fastener failure due to overloading or inadequate clamping forces. Corrosion can also cause fastener failure due to metal fatigue and other environmental factors. Finally, overloading can cause fastener failure due to excessive tension or shear forces.
Prevention of Fastener Failure
In order to prevent fastener failure, it is important to follow proper procedures when selecting and installing fasteners. The first step is to select the right type of fastener for the application. The selection should be based on the application’s requirements, such as the load, environment, and material type. The next step is to use the correct tools and techniques to ensure proper installation. This includes using a torque wrench to ensure the correct level of tightness. Finally, it is important to inspect the fasteners on a regular basis to ensure that they are still in good condition and functioning properly.
Fastener Failure Analysis
Fastener failure analysis is the process of determining the cause of the failure. This involves examining the failed fastener, the surrounding material, and any other relevant evidence. The analysis typically includes a visual inspection of the failed fastener, a measurement of the forces acting on the fastener, and a comparison of the failed fastener to similar fasteners that have not failed. The analysis can also include a determination of the root cause of the failure, such as improper installation, inadequate tightening, incorrect fastener design, corrosion, fatigue, or overloading.
Fastener Failure Modes
Fastener failure can occur in a variety of ways, depending on the type of fastener, the environment, and the load. The most common failure modes are pull-through failure, shear failure, and fatigue failure. Pull-through failure occurs when the fastener becomes loose due to inadequate tightening or incorrect installation. Shear failure occurs when the fastener is overloaded and the shear forces exceed the fastener’s capacity. Fatigue failure occurs when the fastener is subjected to repeated loading and the fatigue life of the fastener is exceeded.
Fastener Pull Through Failure
Pull-through failure is one of the most common types of fastener failure. It occurs when the fastener is not properly tightened or installed and becomes loose due to the load on the fastener. This can be caused by inadequate tightening, incorrect installation, incorrect fastener design, or incorrect material selection. It is important to ensure that the correct fastener type, size, and material is used for the application in order to prevent pull-through failure.
You may also want to learn about what are fasteners and the types of metal fasteners.
Best Practices for Avoiding Fastener Failure
In order to prevent fastener failure, it is important to follow best practices when selecting and installing fasteners. The first step is to select the right type of fastener for the application. The selection should be based on the application’s requirements, such as the load, environment, and material type. The next step is to use the correct tools and techniques to ensure proper installation. This includes using a torque wrench to ensure the correct level of tightness. Finally, it is important to inspect the fasteners on a regular basis to ensure that they are still in good condition and functioning properly.
Testing and Inspection Methods for Fastener Failure
Testing and inspection methods are used to detect and diagnose fastener failure. These methods include visual inspection, magnetic particle testing, radiographic testing, ultrasonic testing, and load testing. Visual inspection is used to identify any visible signs of fastener failure, such as corrosion, wear, or cracks. Magnetic particle testing is used to detect any cracks or other defects in the fastener. Radiographic testing is used to detect any invisible defects in the fastener. Ultrasonic testing is used to detect any internal defects in the fastener. Finally, load testing is used to measure the load on the fastener and determine the cause of failure.
Case Studies of Fastener Failure
Case studies of fastener failure can provide valuable insight into the causes and prevention of fastener failure. One such case study is the failure of a high-pressure nozzle on a gas turbine engine. The nozzle failed due to inadequate tightening of the fastener, which caused the nozzle to become loose and eventually fail. The cause of the failure was identified as incorrect installation of the fastener, which resulted in inadequate tightening. As a result, the proper tools and techniques were used to ensure the proper installation of the fastener and prevent future failures.
Conclusion
Fastener failure is a serious issue that can lead to serious consequences, such as equipment damage, property damage, and even loss of life. It is important to understand the causes and prevention of fastener failure in order to ensure the safety and reliability of the structure. The most common causes of fastener failure are improper installation, inadequate tightening, incorrect material selection, incorrect fastener design, corrosion, fatigue, and overloading. In order to prevent fastener failure, it is important to follow best practices when selecting and installing fasteners. This includes using the correct tools and techniques to ensure proper installation, as well as regular inspection and testing to detect any potential issues. By following these best practices, you can help reduce the risk of fastener failure and ensure the safety and reliability of your structure.
Disclaimer: This article is intended for informational purposes only and does not constitute professional advice. Always consult with a licensed contractor or construction professional for your specific needs.
1 Comment