In the aerospace sector, the margin for error is infinitesimal. Whether you’re talking about commercial aeroplanes, military jets, or spacecraft, each component—down to the last screw—needs to meet the industry’s stringent standards for safety, durability, and performance. This article aims to shed light on the best screws and fasteners crucial for aerospace applications.
Table of Contents
Aerospace Screws
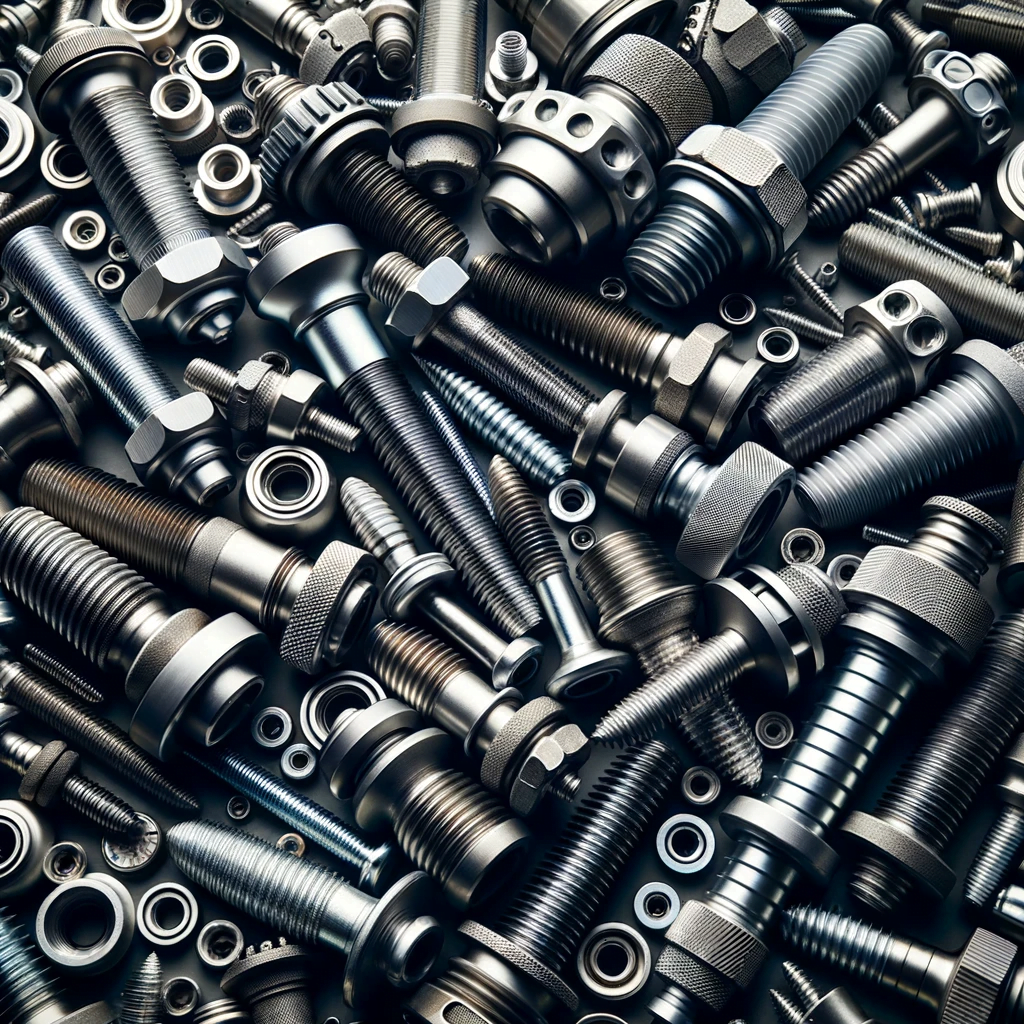
Aerospace screws are the unsung heroes that maintain the structural integrity of aircraft. These fasteners are specially engineered to withstand extreme conditions like high-altitude air pressure and temperature variances. Most aerospace screws are made from alloys such as titanium and Inconel, designed for high tensile strength and corrosion resistance.
Common Types of Aerospace Screws
Machine Screws
Machine screws are a mainstay in the aerospace industry, particularly for connecting metal parts. They come with a variety of head types, including flat, round, and oval, and feature a straight shank with a uniform diameter. The defining attribute of machine screws is their ability to withstand substantial loads and stresses, making them ideal for securing components in aircraft engines, wings, and landing gears. These screws are generally made from high-strength materials like titanium or Inconel to resist the impact of high-altitude pressures and extreme temperatures.
Self-Tapping Screws
Self-tapping screws are uniquely designed to form their own threads as they are driven into pre-drilled holes, making them especially useful in aluminum assemblies. Given aluminum’s lighter weight, it’s often used in aerospace for non-critical structural parts. Self-tapping screws remove the need for a separate tapping operation, speeding up the assembly process. This type of screw is often coated with corrosion-resistant materials to prolong its lifespan, making it a cost-effective and time-saving option in both aircraft and spacecraft applications.
Hex Head Screws
Hex head screws are characterized by their hexagonal-shaped heads, offering a greater torque capacity when compared to other screw types. This makes them particularly useful for applications requiring a secure, tight connection. These screws are frequently used in aerospace applications that involve high-stress and high-pressure environments, like securing aircraft engines or fastening structural elements of the fuselage. Their ability to handle higher torque allows for a more secure fit, ensuring the safety and structural integrity of the aircraft or spacecraft.
You may want to read more about the screw head types.
Aviation Screws
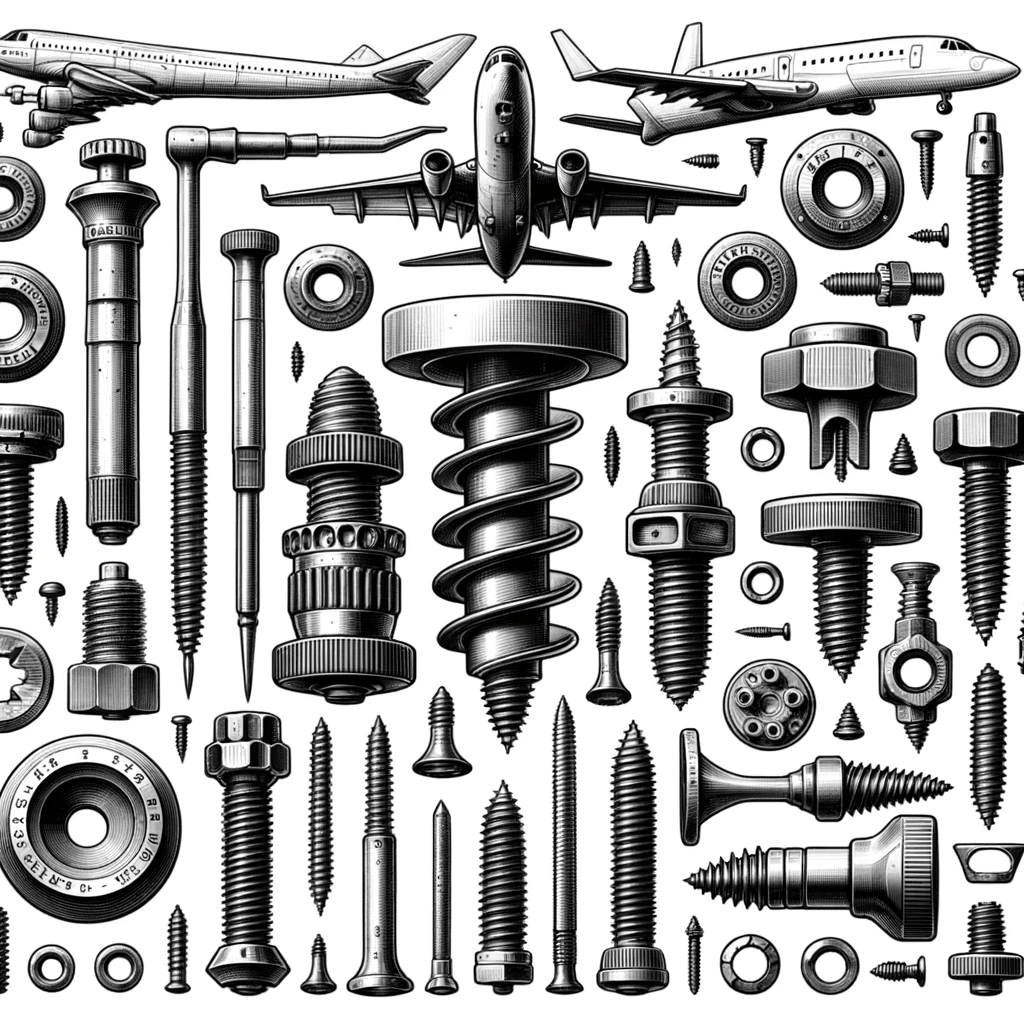
Aviation screws are closely related to aerospace screws but are generally used for the assembly and maintenance of commercial and cargo planes. These screws need to comply with Federal Aviation Administration (FAA) regulations.
Common Types of Aviation Screws
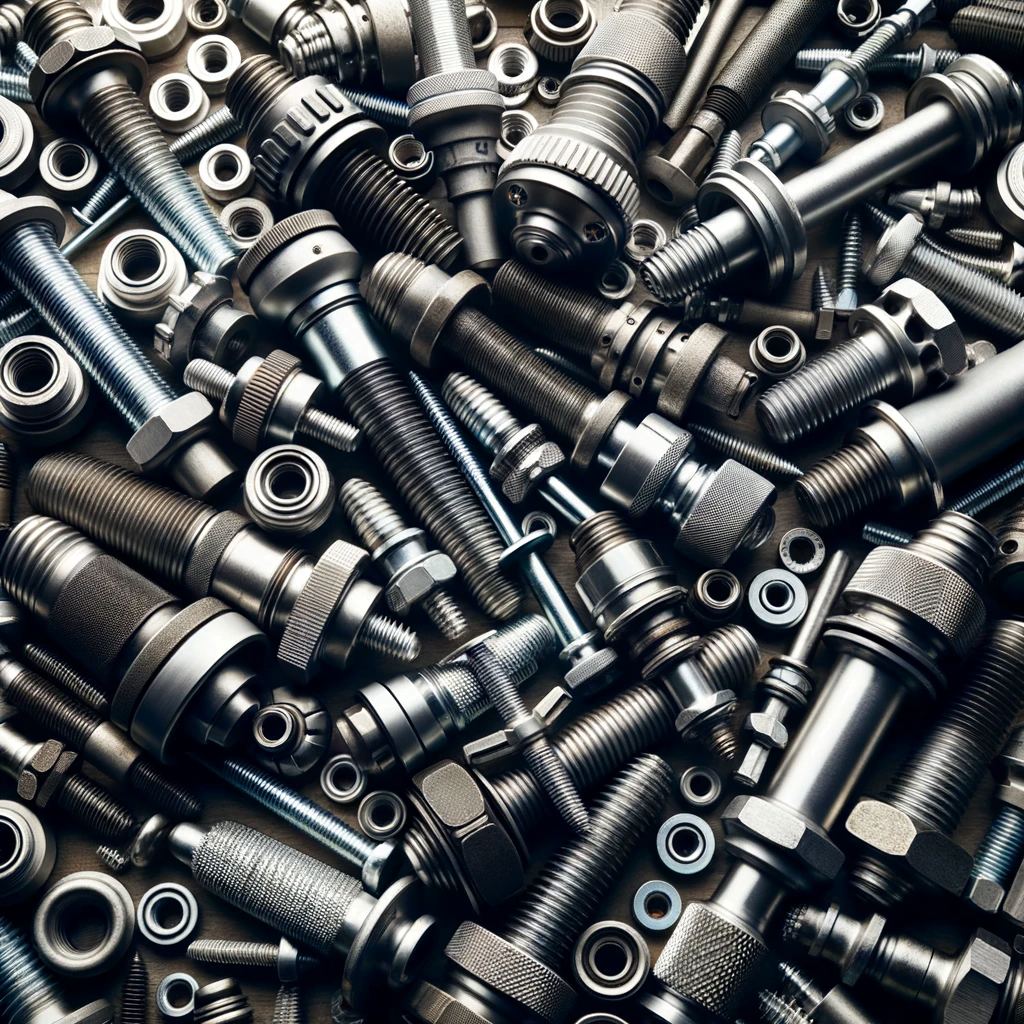
Pan Head Screws
Pan head screws are distinguished by their rounded tops and flat bearing surfaces. They are a staple in aviation, especially when it comes to securing cockpit instrumentation. Their design allows for a balanced distribution of load, providing a secure grip that is crucial for the sensitive electronics and gauges pilots rely on. The rounded head offers aesthetic benefits while still serving a functional purpose, ensuring that no sharp edges are protruding, which could be hazardous in the confined space of a cockpit. They are often manufactured from materials that resist vibration and thermal expansion, such as aerospace-grade aluminum alloys or high-strength steel.
Flat Head Screws
Flat head screws sit flush against the surface they are fastened to, making them an excellent choice for applications where a smooth surface is required. In aviation, they are commonly found in interior panels, overhead compartments, and seat assemblies. Their flush-fitting design is not just aesthetically pleasing but also minimizes aerodynamic drag, which is a critical consideration in aviation. The flat head design often accompanies a countersunk hole, ensuring that the screw fits perfectly flush with the surface. Made typically from corrosion-resistant materials like titanium, they are built to last, resisting the wear and tear of constant flights and variable atmospheric conditions.
Shoulder Screws
Shoulder screws, also known as stripper bolts, feature a cylindrical, unthreaded shoulder between the head and the threaded section. They are particularly valuable in aviation for securing movable assemblies like landing gears, flaps, and mechanical linkages. The unthreaded shoulder allows for a degree of rotation, providing the necessary freedom of movement for components that require precise alignment and positioning. These screws are designed to take on both axial and radial loads, making them ideal for complex mechanical systems found in modern aircraft. The materials used for shoulder screws in aviation are typically high-strength alloys that can withstand extreme pressure and temperature fluctuations.
Aerospace Ball Screws
Ball screws in aerospace applications are different from your run-of-the-mill screws. These are specifically used in precision applications like the movement of flight control surfaces and landing gear. They offer high mechanical efficiency and can withstand heavy loads, making them crucial for aircraft and spacecraft alike.
Ball screws are not your typical screws. In the context of aerospace applications, they serve a specialized role that goes beyond merely fastening components. Designed for high precision, reliability, and durability, aerospace ball screws are engineered for some of the most critical tasks onboard an aircraft or spacecraft, such as the movement of flight control surfaces like ailerons and flaps, as well as the extension and retraction of landing gear systems.
In the world of aerospace, the engineering specifications for ball screws are exceedingly stringent. They must offer high mechanical efficiency, typically above 90%, to minimize the energy loss during operation. This is critical because even a slight inefficiency can have significant ramifications when dealing with the fuel limitations and payload constraints of an aircraft or spacecraft.
These ball screws are constructed from advanced materials like specialized steel alloys or even ceramic composites to ensure they can withstand heavy loads, extreme temperatures, and corrosive environments. The materials are typically heat-treated to improve their mechanical properties further and might undergo several quality control tests to ensure their strength and precision.
Another aspect that sets aerospace ball screws apart from their industrial counterparts is the attention to their wear resistance. Given the life-or-death importance of their roles, these screws often feature a fortified design to reduce friction and prolong their lifespan. This includes advanced forms of lubrication and, in some cases, the integration of redundant systems as a fail-safe.
Moreover, the development of aerospace ball screws usually involves extensive computational simulations, physical testing, and collaboration with aerospace engineers. The final products often need to receive certification from aerospace regulatory bodies, such as the Federal Aviation Administration (FAA) in the United States or the European Union Aviation Safety Agency (EASA) in Europe, before they can be incorporated into aircraft or spacecraft systems.
In summary, aerospace ball screws are indispensable elements in the aviation and space sectors. They are designed to meet some of the most rigorous engineering standards to ensure safety, efficiency, and longevity, making them crucial for the performance and reliability of both aircraft and spacecraft.
Captive Screw Aerospace
The idea behind a captive screw is that it remains permanently attached to the assembly, even when loosened. These screws are often used in applications that require frequent removal and reinsertion. Their primary advantage is that they reduce the risk of lost or misplaced screws, which is vital in aerospace applications.
The unique feature of captive screws, that sets them apart from other types of screws, is their design that allows them to stay permanently affixed to the assembly or component they are a part of, even when they are loosened or unfastened. This is a particularly useful attribute in aerospace applications, where the stability and security of each component are of utmost importance.
Aerospace applications often involve complex assemblies with multiple parts that may require regular maintenance, inspection, or adjustments. Given the high-stakes environment of aerospace—where a lost or misplaced screw could lead to catastrophic consequences—the use of captive screws becomes particularly significant. Their primary advantage lies in the assurance they offer against such risks. Even during frequent removal and reinsertion processes, captive screws remain attached to their parent component, thereby reducing the potential for human error, which is always a concern in aerospace settings.
The design of captive screws often includes a retainer mechanism, which might be a separate component or integrated into the screw itself. This mechanism locks the screw into place, ensuring it remains with the assembly even when loosened. This is not just a convenience feature but a critical safety measure, especially in applications like securing access panels, instrumentation consoles, and other systems that technicians and engineers interact with regularly.
Additionally, captive screws in aerospace applications are often made of high-strength, corrosion-resistant materials like titanium or specialized steel alloys. These materials have to undergo rigorous testing for tensile strength, corrosion resistance, and thermal stability. Any sub-standard screw can be a point of failure in an aerospace application, making the quality of captive screws non-negotiable.
The manufacturing and utilization of captive screws in aerospace are highly regulated. They must adhere to various standards such as the Aerospace Material Specification (AMS) or even military specifications when used in military aerospace applications. Every batch of screws typically goes through stringent quality control procedures, often involving X-ray inspections, to ensure they meet the necessary specifications and tolerances.
In summary, captive screws in aerospace applications offer a two-fold benefit—convenience and safety. Their design minimizes the risks associated with the loss or misplacement of screws, a feature that becomes critically important given the sensitive and complex nature of aerospace assemblies.
Aerospace Socket Set Screws
Aerospace socket set screws are generally used for securing an object within or against another object. Made of materials like A286 stainless steel, they are often used in engine assemblies and critical aircraft systems.
Aerospace socket set screws are specialized fasteners designed to secure one object within or against another. While the function might sound simple, the role they play in aerospace applications is far from trivial. These screws are a cornerstone in critical systems where precision, reliability, and strength are paramount, such as in engine assemblies, fuel systems, and various other crucial aircraft mechanisms.
The material choice for these screws often leans towards high-performance alloys, with A286 stainless steel being a prominent example. This material provides a unique combination of corrosion resistance, high-temperature stability, and excellent tensile strength. Because aerospace components are exposed to a wide range of temperatures and pressures, from the cold vacuum of space to the heat of jet engines, the materials must be rigorously tested and vetted for their durability and resilience. A286 stainless steel often meets or exceeds these stringent requirements, making it an ideal material for aerospace socket set screws.
These screws are generally used in engine assemblies, where they might secure fan blades to the rotor, or lock in various other components that make up complex engine systems. Given the extreme operational conditions within an aircraft engine—high rotational speeds, tremendous heat, and corrosive by-products—the use of high-quality socket set screws is non-negotiable. Any failure in this context could be catastrophic, making the role of these seemingly inconspicuous components highly critical.
Additionally, aerospace socket set screws are often treated with specialized coatings for extra protection against elements like oxidation and wear. These coatings not only improve the longevity of the screws but also minimize the chances of galling, a form of wear caused by adhesion between sliding surfaces. This is particularly important when the screws are used in moving parts or assemblies that require frequent adjustments.
It’s also worth mentioning that aerospace socket set screws must adhere to a range of compliance standards and specifications. They undergo meticulous quality control checks, often involving non-destructive testing methods like ultrasonic inspection or X-ray fluorescence, to ensure they meet the rigorous aerospace application requirements.
In summary, aerospace socket set screws are not your ordinary set screws; they are highly engineered components crafted to meet the strictest standards of the aerospace industry. Their role in ensuring the secure and reliable functioning of aircraft and spacecraft systems underscores their importance, making them indispensable elements in modern aerospace applications.
Conclusion
The aerospace industry demands fasteners that meet exacting specifications. Choosing the right kind of screw or fastener not only ensures the structural integrity of the aircraft but also guarantees the safety of those on board. The types of screws discussed in this article are designed to meet these demands, and opting for anything less is not an option.
When you are selecting screws and fasteners for aerospace applications, consider the materials, design specifications, and compliance standards. The safety and efficacy of our skies depend on these small but crucial components.
No Comments