Whether you’re working on a home improvement project, an automotive repair, or an industrial assembly, knowing how to measure a screw size is essential. The task may seem straightforward, but there are numerous nuances that can make all the difference in getting the right fit. In this comprehensive guide, we’ll walk you through the process of measuring screw sizes using various methods and tools, from calipers to gauge charts.
Table of Contents
The Importance of Accurate Measurements
Getting the screw size wrong can lead to various issues, from structural instability to the sheer waste of time and resources. Therefore, knowing how to measure screw size is crucial for any DIYer, mechanic, or professional.
The Importance of Accurate Measurements in Screw Sizing
The correct measurement of screw sizes is far more than a trivial detail; it’s a critical element that influences the integrity and functionality of the entire project or repair work. Inaccurate measurements can have a wide range of negative consequences, each of which underscores the importance of getting the sizing right from the start.
Structural Integrity
Firstly, using screws of the wrong size can compromise the structural integrity of the object you’re working on, be it a piece of furniture, automotive part, or a construction project. Screws that are too large for a given hole may crack the material, while screws that are too small may not provide sufficient hold. In either case, the end result is a weakened structure that could fail under stress or over time.
Resource Wastage
Inaccurate screw measurements also lead to the waste of valuable resources. Using the wrong screws means you’ll likely need to replace them, which not only wastes the screws themselves but also the materials into which they were inserted. Over time, these costs can add up, impacting the overall budget of your project or repair work.
Time Consumption
The time spent identifying and correcting screw size mistakes is time that could be used more productively elsewhere. If you’re working on a tight schedule, such delays could be costly. They may lead to missed deadlines, which in turn could result in financial penalties or lost opportunities.
Professional Reputability
For mechanics, builders, and other professionals, using the wrong screw size can also tarnish their reputation. Attention to detail is a highly valued skill in these professions, and failure to measure screws accurately can suggest a lack of expertise or care, potentially affecting future business.
Safety Concerns
Last but not least, safety is a significant concern. Incorrectly sized screws could lead to the failure of critical components, posing risks of injury or even catastrophic failure in extreme cases. Therefore, accurate screw measurements are not just a matter of professional competence but also a safety imperative.
In summary, knowing how to measure screw size accurately is a crucial skill set that impacts the structural integrity, resource allocation, time management, professional reputation, and safety of any project. It’s an indispensable competency for DIY enthusiasts, mechanics, and professionals alike.
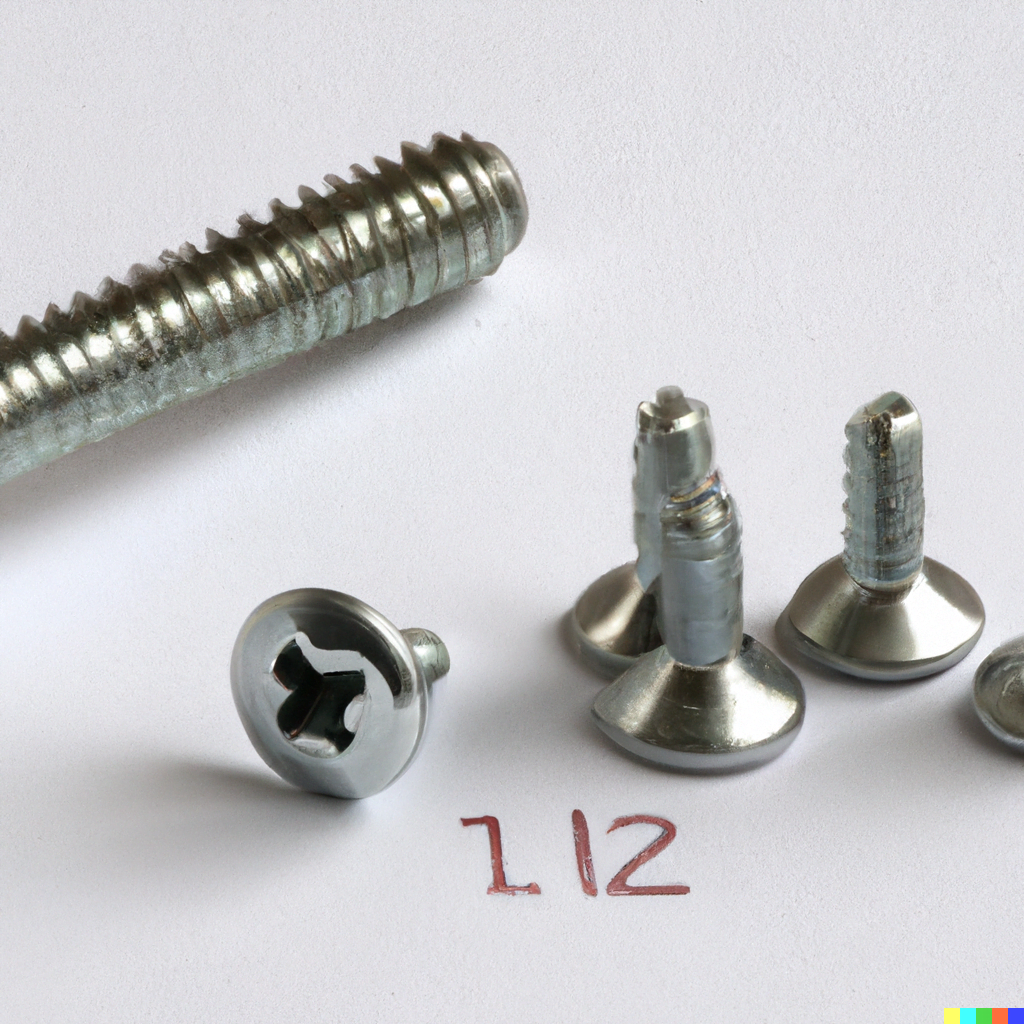
Basic Terminology
Before diving into the measurements, it’s essential to familiarize yourself with some basic terminology:
- Diameter: The thickness of the screw.
- Thread Count: Number of threads per inch or millimeter.
- Length: The length of the screw from the tip to the underside of the head.
- Head Size: The size of the screw’s head.
Basic Terminology in Screw Measurement
Before you can effectively measure a screw, it’s essential to understand the various components and terms used to describe its dimensions. Having a solid grasp of these basic terms will not only help you in the measurement process but also ensure you can accurately communicate your needs, whether you’re purchasing screws or discussing specifications with colleagues.
Diameter
The diameter of a screw refers to the width of the screw shaft at its widest point. This measurement is critical because it determines the screw’s fitting into the material you’re fastening. The diameter is usually measured in millimeters (mm) or inches (in), depending on the standard used. To get the most accurate measurement, it’s best to use calipers, especially for smaller screws where a slight difference in diameter can make a significant impact.
Thread Count
The thread count tells you the number of threads per unit length on the screw shaft. This could be threads per inch (TPI) in the Imperial system or threads per millimeter (TPM) in the Metric system. The thread count affects both the screw’s holding strength and how finely it can be adjusted when tightened or loosened. This measurement is crucial for screws used in applications that require a high level of precision or where the material being fastened has specific tolerances.
Length
The length of a screw is the distance from the very tip of the screw to the underside of the head (the side that will sit flush against the material when fully inserted). Knowing the right length is crucial for ensuring that the screw penetrates deep enough to hold but not so deep that it damages the material or passes through it completely. Like diameter, length is generally measured in inches or millimeters.
Head Size
Head size refers to the dimensions of the screw head, which can come in various shapes and sizes like flat, pan, or dome-shaped. This measurement is important for several reasons. A larger head size generally provides more surface area, distributing the pressure more evenly and thus increasing holding strength. However, the size and type of screw head you need can also depend on aesthetic considerations or constraints of the material you’re working with.
Tools Required for Measuring
- Calipers: For precise measurements.
- Ruler or Tape Measure: For basic measurements.
- Screw Gauge: To determine the thread count.
- Thread Pitch Gauge: For identifying thread size.
Tools Required for Measuring Screw Dimensions
When it comes to measuring screws, having the right tools on hand is essential for both accuracy and efficiency. Below are the standard tools commonly used for measuring different aspects of screws:
Calipers
Calipers are a highly precise measuring tool commonly used for determining the diameter and length of screws. There are various types, such as digital and vernier calipers, each offering its own level of accuracy. Calipers are especially useful when dealing with smaller screws or screws requiring exact measurements, such as those used in specialized machinery or electronics. They can measure dimensions to the nearest thousandth of an inch or millimeter, providing a high level of accuracy that other tools may not offer.
Ruler or Tape Measure
While not as precise as calipers, rulers and tape measures are more accessible and sufficient for less critical applications. They are mainly used for measuring the length of screws. However, for smaller screws or those requiring tight tolerances, a ruler may not provide the needed level of precision. In casual or DIY settings where exact measurements aren’t critical, a ruler or tape measure can be a convenient choice.
Screw Gauge
A screw gauge is specifically designed to measure the thread count on a screw. This tool typically comes with multiple leaves or blades, each with a different thread count marked on it. By fitting these blades into the screw’s threads, you can determine the number of threads per inch or per millimeter. Knowing the thread count is crucial for selecting the right screw for applications requiring a specific level of holding strength or adjustability.
Thread Pitch Gauge
The thread pitch gauge is another specialized tool for identifying the size and type of threads on a screw. Unlike a screw gauge that focuses on thread count, the thread pitch gauge measures the angle and spacing between the threads. This is particularly important for screws used in specialized applications, where the thread pitch can significantly affect the screw’s performance.
The Steps in Measuring Screw Size
Basic Measurement
- Measuring Diameter: Use a caliper to measure the screw’s diameter. This measurement is often represented in millimeters or inches.
- Measuring Length: Measure the length from the tip to the base of the head.
- Thread Count: Using a screw gauge, determine the number of threads per inch.
The Basics of Screw Measurement
When it comes to screws, obtaining accurate measurements is fundamental for a variety of applications, be it construction, machinery repair, or any DIY project. Here are the key dimensions you need to measure:
Measuring Diameter
The diameter is one of the most crucial dimensions of a screw. It informs you of the width of the screw’s shaft, determining its compatibility with the material into which it will be inserted. A caliper is the recommended tool for this task, as it provides high-precision measurements. The diameter is typically represented in millimeters (mm) when using the Metric system or inches (in) when using the Imperial system. Make sure to measure at the widest point of the screw, avoiding the threads, to get an accurate reading.
Measuring Length
The length of a screw is another essential measurement, defining how deep the screw will penetrate into the material. To measure the length, start from the very tip of the screw and go all the way to the base of the head, not the top. This ensures that you get a reading that reflects the part of the screw that will actually be embedded into the material. While a ruler or tape measure can be used for this, calipers will give you a more precise measurement, especially for smaller screws.
Thread Count
The thread count is a measure of how many threads appear per unit length on the screw’s shaft. This is especially important for applications requiring specific holding strength or adjustability. A screw gauge is the ideal tool for this task, equipped with various blades that each represent a different thread count. Simply match the screw threads with the appropriate blade to determine the number of threads per inch or per millimeter.
Advanced Methods
- Measuring Screw Hole Size: Insert a screw with known dimensions into the hole and measure the fit.
- Measuring with Calipers: For a more precise measurement, use calipers to measure the diameter, length, and thread pitch.
Advanced Methods of Screw Measurement
For applications requiring more stringent measurements, advanced methods can provide the degree of precision necessary to ensure a project’s success. Let’s delve into some of these techniques:
Measuring Screw Hole Size
Knowing the size of the hole where the screw will be inserted is paramount, especially in applications that require a tight fit for structural integrity. One approach to gauge this is by using a screw with known dimensions as a test. Insert the screw into the hole and assess how well it fits. It should neither be too loose nor too tight. A screw that’s too loose won’t hold well, while a too-tight fit could lead to material damage. This trial-and-error approach can be very effective in determining the exact size needed for the application at hand.
Measuring with Calipers
Calipers offer the pinnacle of precision when it comes to measuring screw dimensions. Unlike basic rulers or tape measures, calipers can provide measurements down to the nearest thousandth of an inch or millimeter. This level of accuracy is crucial in specialized fields such as aerospace, medical devices, or precision machinery. With calipers, you can measure not just the diameter and length of the screw, but also the thread pitch, which is the distance between the threads. This provides a comprehensive understanding of the screw’s dimensions, ensuring that it is the perfect fit for the application you have in mind.
Measuring Specific Types of Screws
- Allen Screw Size: Measure the distance across the flat sides of the screw’s head.
- Grub Screw Size: Measure the outside diameter and the length.
- Hex Screw Size: Measure across the flats for the width and from tip to underside for length.
- Machine Screw Size: Use a ruler for a basic measurement, or calipers for greater accuracy.
- Wood Screw Size: Measure the major diameter and the length.
- Metric Screw Size: Measurements are taken in millimeters.
- UK Screw Size: Similar to metric, but sometimes featuring unique British standard sizes.
Measuring Specific Types of Screws
The way you measure a screw can differ depending on its type, as each type of screw is designed for a specific purpose and thus has unique features worth measuring. Let’s look into some commonly used types:
Allen Screw Size
For Allen screws, which are often used in machinery or furniture assembly, it’s critical to measure the distance across the flat sides of the screw’s hexagonal head. This is known as the “across-flats” dimension and can be precisely measured using calipers. Accurate measurement ensures you use the correct Allen wrench for installation or removal.
Grub Screw Size
Grub screws, often used in securing rotating elements like pulleys or gears to a shaft, are usually headless. Therefore, the primary dimensions to measure are the outside diameter and the length of the screw. These can be measured using calipers for a precise fit.
Hex Screw Size
Hex screws are named for their hexagonal heads and are commonly used in construction and machinery. To measure these screws, you’ll need to measure across the flats (the distance from one flat surface of the hexagon to the opposite flat surface). Additionally, the length is measured from the tip of the screw to the underside of the hexagonal head, not to the top.
Machine Screw Size
Machine screws are primarily used in machinery and appliances. For basic needs, a ruler can be used to measure both the diameter and length. However, for more precise applications, calipers should be used for the most accurate measurements, especially when measuring thread pitch.
Wood Screw Size
Wood screws are primarily used in woodworking projects. To measure a wood screw, focus on the major diameter (the largest diameter of the threaded part) and the length from the tip to the underside of the head. This ensures that the screw will provide the holding power needed for your woodworking project.
Metric Screw Size
When working with metric screws, all measurements are taken in millimeters, including diameter, length, and thread pitch. This is often the standard in countries using the metric system and in specific industries like automotive and scientific research.
UK Screw Size
UK screw sizes are similar to metric measurements but can sometimes feature unique British standard sizes, especially for historical or specialized applications. Therefore, it’s important to double-check whether a screw adheres to metric or British standards.
Frequently Asked Questions
- How to Measure Torx Screw Size?: Use specialized Torx gauges.
- How to Measure Screw Size in MM?: Use a metric ruler or calipers.
- What Size Screw Do I Need?: Measure the hole size and depth to determine this.
Knowing how to measure the size of a screw is essential for a variety of tasks. With the right tools and a keen eye for detail, you can quickly and accurately determine the size of any screw, be it a wood screw, machine screw, or specialized set screw. With this guide, you are well-equipped to handle any screw-measuring task that comes your way.
No Comments