In the world of maritime engineering and construction, the devil is truly in the details. One such critical detail that often doesn’t get the attention it deserves is the selection of appropriate fasteners. It’s not merely a mechanical decision but a pivotal one that directly influences both the safety and the longevity of marine structures. Given that these structures—be it boats, yachts, docks, or offshore platforms—are constantly battered by the elements, the significance of choosing the right kind of fasteners is magnified exponentially. Among these, marine fasteners and screws stand out for their exceptional ability to withstand the harsh saltwater conditions that would cause standard fasteners to fail.
In this comprehensive guide, we go beyond the surface to explore the complex world of marine fasteners in-depth. We’ll cover a broad spectrum of fasteners specifically engineered for marine applications, such as stainless steel marine screws that offer superior corrosion resistance, and marine-grade 316 stainless steel screws that are designed to perform optimally even in the most corrosive environments. This guide also includes insights into other specialized marine fasteners, each designed to meet a unique set of requirements and challenges presented by life at sea or along the coastline.
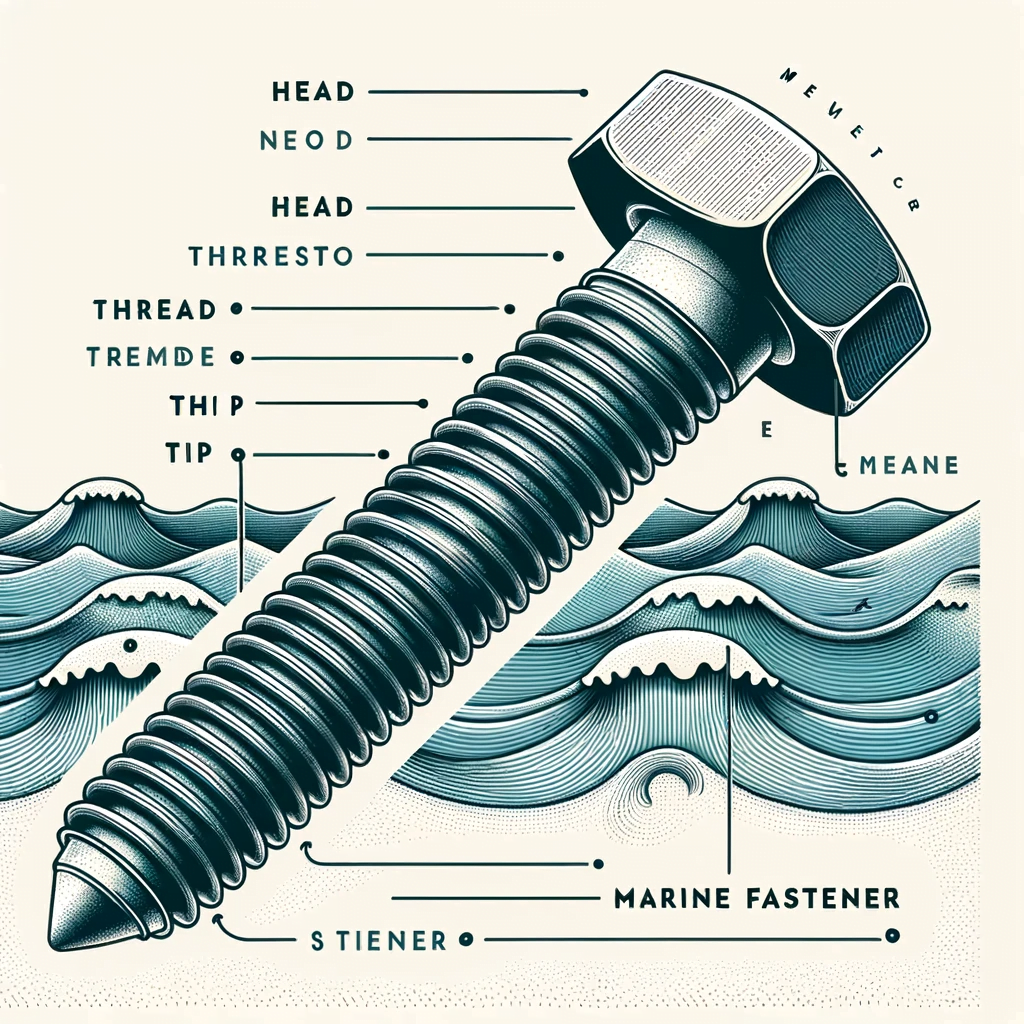
Through this exploration, we aim to provide you with the knowledge and tools you need to make informed decisions when selecting marine fasteners for your next project. Whether you are a seasoned marine engineer, an avid boater, or someone venturing into maritime applications for the first time, understanding the intricacies of these vital components can make the difference between a structure that stands strong in the face of Mother Nature’s wrath and one that succumbs to the corrosive, erosive, and often unpredictable forces at play in marine environments.
So, let’s dive right in and unravel the intricacies of marine-grade fasteners, enabling you to navigate through choices that could very well determine the long-term success and safety of your maritime endeavors.
Table of Contents
Why Specialty Marine Fasteners are Essential
Typical screws and bolts are not designed to withstand the corrosive nature of marine environments. Enter marine fasteners, the unsung heroes that bear the brunt of nature’s forces, ensuring the structural integrity of vessels, marinas, and offshore platforms.
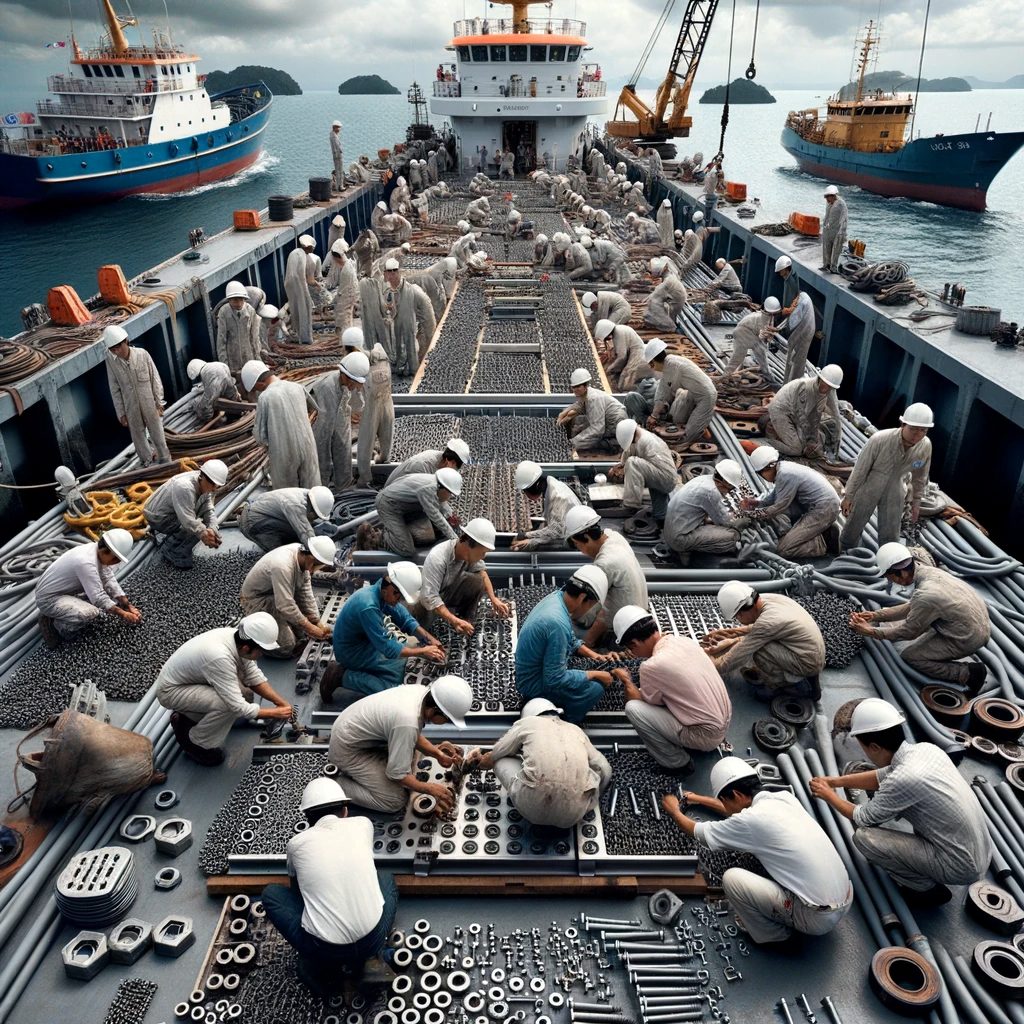
The importance of marine fasteners in any maritime application cannot be overstated. While conventional screws and bolts may suffice for indoor or less corrosive environments, they fall woefully short when exposed to the harsh conditions of the sea. The maritime world is an arena of extremes, where high levels of salinity, fluctuating temperatures, and persistent moisture converge to create a breeding ground for corrosion. Traditional fasteners are not engineered to combat these challenges, leaving them susceptible to rapid deterioration and, in worst-case scenarios, catastrophic failure.
In contrast, specialty marine fasteners serve as the unsung heroes of maritime construction and repair, steadfastly bearing the brunt of nature’s forces. These fasteners are meticulously designed and manufactured to ensure the structural integrity of a wide range of marine installations—from leisurely yachts and fishing boats to heavy-duty marinas and offshore oil platforms. Their primary role is to securely join materials while offering heightened levels of corrosion resistance, thereby extending the overall lifespan of marine structures.
When you consider the vast responsibilities that rest on marine infrastructure—be it commercial, recreational, or even lifesaving—it becomes abundantly clear why compromising on fastener quality is not an option. Inferior fasteners not only risk the integrity of individual components but also jeopardize the safety and functionality of the entire structure. Whether it’s a dock that accommodates hundreds of boats or an offshore rig that drills deep into the ocean floor, the failure of even a single fastener could lead to disastrous consequences.
Therefore, opting for specialized marine-grade screws, bolts, and other types of fasteners is a critical, non-negotiable aspect of maritime construction and maintenance. These components are crafted to meet stringent quality standards, ensuring they can robustly stand up to the relentless conditions they are exposed to. It is this level of uncompromising quality that makes marine fasteners invaluable assets in the fight against the elements, guaranteeing long-term durability and, ultimately, peace of mind.
You may want to read also about how to measure screw size.
Marine Grade Screws: The Cornerstone of Marine Construction
Marine grade screws, including marine stainless steel screws and marine wood screws, are specifically designed to withstand the aggressive corrosion from saltwater exposure.
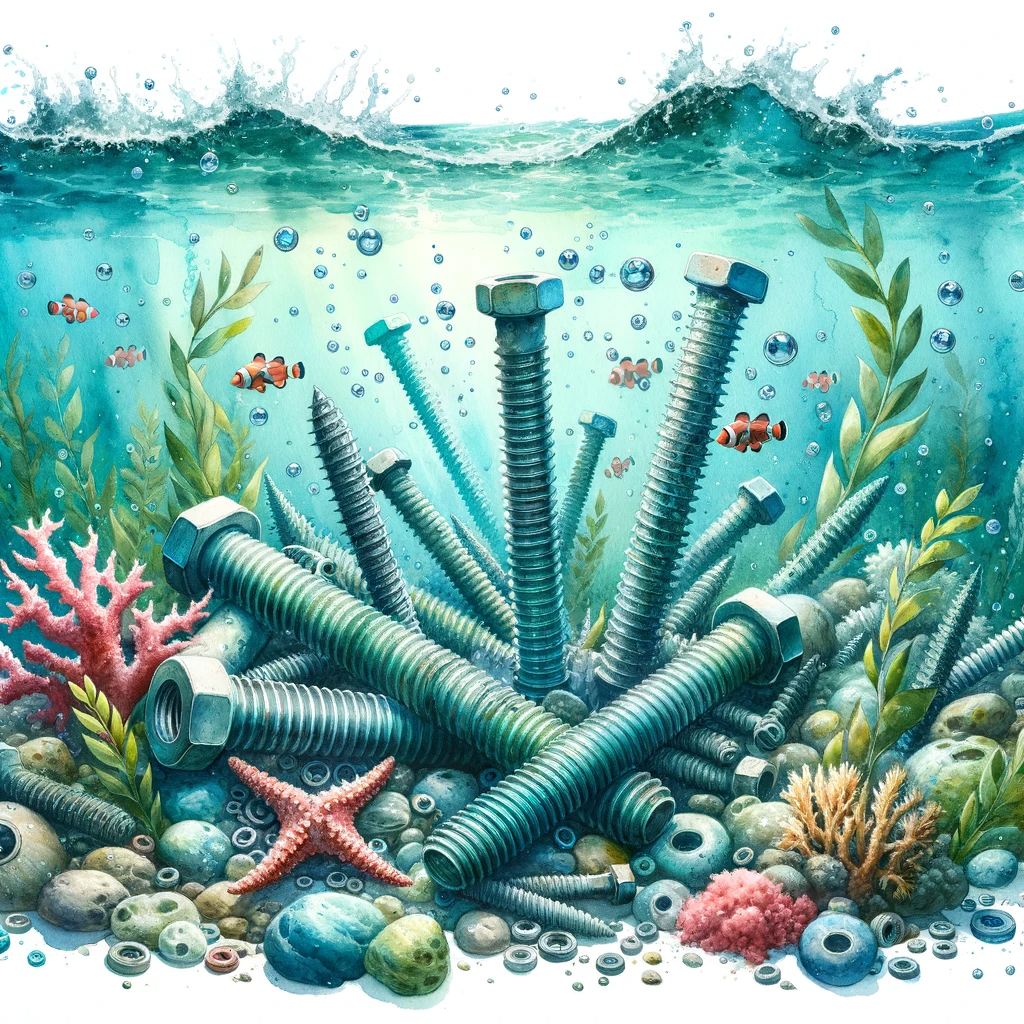
Marine grade screws are more than just a category; they are the cornerstone upon which resilient and lasting marine structures are built. Unlike their standard counterparts, marine grade screws are engineered with a singular purpose: to stand up against the relentless corrosive forces posed by saltwater environments. This entails not just surviving, but thriving under conditions that include aggressive corrosion, extreme weather fluctuations, and constant exposure to moisture.
When one speaks of marine grade screws, it’s important to recognize the diverse sub-categories within this group, each designed to meet specialized needs. One of the most commonly employed varieties are marine stainless steel screws. These fasteners are manufactured from high-grade stainless steel, typically 316 grade, which is renowned for its excellent resistance to rust and corrosion. These screws are often used in critical structural applications, including the assembly of boat hulls, piers, and even offshore oil rigs.
Then, we have marine wood screws, another crucial sub-category. These are specifically tailored for applications involving wooden materials, such as boat decks, wooden piers, and other marine-related wooden structures. What makes them unique is their ability to not only resist the corrosive elements but also to minimize wood splitting, thanks to their unique design features like tapered heads and special thread forms.
It’s essential to remember that saltwater is an unforgiving environment, laden with minerals and saline that can break down weaker materials with ease. Standard screws may work temporarily but will eventually succumb, leading to structural integrity issues and necessitating costly repairs or replacements. Marine grade screws, on the other hand, provide the kind of steadfast reliability that engineers, architects, and marine professionals rely on for constructing durable and safe maritime structures.
In summary, marine grade screws serve as the foundational building blocks for any durable and long-lasting marine construction project. Whether it’s marine stainless steel screws for heavy-duty structural applications or marine wood screws for aesthetic yet sturdy wooden fixtures, these specialized fasteners are indispensable in providing the security and longevity required to withstand the harsh marine conditions that standard screws simply cannot handle.
Marine Grade 316 Stainless Steel Screws: The Gold Standard in Durability and Resistance
When it comes to the pinnacle of durability, marine-grade 316 stainless steel screws are the fasteners of choice. With the inclusion of molybdenum, they offer superior resistance to chlorides found in marine environments.
When discussing marine grade screws, it would be remiss not to delve into the specific advantages of marine-grade 316 stainless steel screws, often considered the gold standard in marine fastening solutions. These screws are not just another option; they represent the epitome of durability and longevity in the world of marine fasteners.
Marine environments present an array of challenges, most notably, the high concentration of chlorides found in saltwater. Chlorides are notorious for their corrosive properties, attacking lesser grades of metal at a microscopic level, leading to rust and eventually structural failure. What sets marine-grade 316 stainless steel screws apart from others is their unique chemical composition, which includes the addition of molybdenum. This special element enhances the material’s resistance to chloride corrosion significantly.
The addition of molybdenum in 316-grade stainless steel results in screws that possess a molecular structure capable of enduring harsh marine conditions for extended periods. It acts as a reinforcing agent, creating a fortified barrier against corrosive agents. This makes these screws ideal for some of the most demanding marine applications, including but not limited to shipbuilding, offshore drilling platforms, and intricate machinery exposed to saltwater.
Furthermore, 316 stainless steel also provides excellent tensile strength, making these screws not only resistant to corrosive elements but also incredibly strong and durable. They are capable of maintaining their integrity under significant stress and load, making them a trustworthy option for structural applications that demand both stability and longevity.
It is the unique combination of these features—superior corrosion resistance and outstanding tensile strength—that has led industry professionals to herald marine-grade 316 stainless steel screws as the fasteners of choice for critical marine applications. With such high levels of durability and resistance, these screws are often viewed as an investment into the long-term sustainability and safety of marine structures.
When the stakes are as high as they are in maritime construction, where the integrity of the entire structure could hinge on the quality of its individual components, settling for anything less than marine-grade 316 stainless steel screws is simply not an option. These screws provide the peace of mind that comes with knowing that the fasteners will not be the weak link in any marine construction venture.
Material Choices for Marine Fasteners
Stainless Steel Marine Fasteners
Selecting the right material for marine fasteners is a nuanced task that requires a deep understanding of the unique challenges posed by maritime environments. It’s not merely a matter of picking the toughest or most corrosion-resistant metal; it involves a multi-faceted approach that considers not just durability but also tensile strength, resistance to specific types of corrosion, and even cost-effectiveness. Here, we’ll delve into the various material options available for marine fasteners and discuss the pros and cons of each to offer a comprehensive guide for informed decision-making.
Stainless Steel Marine Deck Screws
In the realm of marine construction, the importance of choosing the right fasteners cannot be overstated. Among the various types of marine screws, stainless steel marine deck screws stand out as the most preferred option for decking applications. These screws are engineered for excellence, offering attributes that cater specifically to the unique challenges presented by maritime settings.
The first and perhaps most crucial feature of stainless steel marine deck screws is their superior holding power. Decking, whether on a boat or a marina, is subject to constant foot traffic, environmental stress, and shifting weight. All these factors place considerable stress on the fasteners. A deck is only as sturdy as the screws that hold it together, and in this regard, stainless steel marine deck screws excel. Their enhanced tensile strength and design, often featuring deep threads and specialized drive types, ensure that once they are in place, they stay in place, providing a level of security and stability that is unmatched.
Moreover, these screws offer exceptional corrosion resistance, a vital attribute when dealing with the harsh conditions of a marine environment. Constructed from high-quality stainless steel, these screws can withstand prolonged exposure to saltwater, humidity, and other corrosive elements that are common in maritime settings. This level of corrosion resistance is especially crucial for decking applications where the screws will be directly exposed to the elements, making them susceptible to rust and eventual failure if made from inferior materials.
The unique combination of holding power and corrosion resistance in stainless steel marine deck screws makes them ideal for a myriad of decking applications. They are commonly used in boat decks, boardwalks, marina platforms, and even in some outdoor furniture meant for coastal environments. The uniform quality and durability they offer serve to extend the lifespan of marine decking structures, reducing the frequency and cost of maintenance and repairs.
In addition to their technical advantages, stainless steel marine deck screws often come with additional features like self-tapping points and countersinking heads. These make the installation process more straightforward, saving time and labor costs, while ensuring a flush finish that adds to the aesthetic appeal of the deck.
In conclusion, stainless steel marine deck screws are not just another category of fasteners; they are the epitome of what one should seek in a marine decking application. Combining extraordinary holding power with unparalleled corrosion resistance, these screws provide a level of reliability and performance that is essential for any maritime decking project. Their benefits go beyond just structural integrity, extending into ease of installation and long-term cost-effectiveness, making them the go-to choice for professionals in the field.
Brass Marine Screws and Bronze Fasteners Marine
When discussing the materials commonly used for marine fasteners, brass and bronze often make their way into the conversation due to their natural resistance to corrosion. These materials offer a unique combination of properties that make them an attractive choice for specific marine applications. However, it’s essential to understand their limitations, particularly when compared to other materials like stainless steel, which tend to offer higher tensile strength.
Brass and bronze fasteners owe their popularity in marine applications in large part to their inherent corrosion resistance. Both of these metals form a protective oxide layer when exposed to moisture, effectively shielding the material underneath from corrosive elements like saltwater. This corrosion resistance is especially valuable in marine environments, where fasteners are continually exposed to a mix of moisture, salt, and other corrosive substances.
Yet, despite their natural ability to resist corrosion, brass and bronze fasteners are not the go-to choice for every marine application. One of the key reasons for this is their comparatively lesser tensile strength when stacked against stainless steel options. While brass and bronze are undoubtedly durable, they can’t match the tensile strength provided by high-grade stainless steel fasteners. Tensile strength is a critical factor when it comes to structural integrity and the ability to withstand heavy loads and stresses, common conditions in maritime settings.
Due to these limitations in tensile strength, the use of brass and bronze fasteners is often confined to specific applications. For example, these materials are commonly used in less load-bearing parts of a marine structure, like decorative features or light fixtures, where high tensile strength isn’t a priority but resistance to corrosion is still vital. They are also used in applications where aesthetic considerations come into play. Brass and bronze offer a classic, timeless appearance that can be an important factor in the overall design of a boat or marine structure.
However, advances in metallurgy and manufacturing techniques have led to alloy variations that seek to bridge the gap between corrosion resistance and tensile strength. These specialized brass and bronze alloys offer a middle-ground solution, albeit usually at a higher cost. Such innovations provide marine engineers and builders with more versatile options when choosing the right material for their specific needs.
In summary, while brass marine screws and bronze fasteners offer excellent natural resistance to corrosion, their application in marine environments is somewhat restricted due to their lesser tensile strength compared to high-grade stainless steel options. However, their aesthetic appeal and specialized alloys make them an attractive choice for particular applications where the highest tensile strength is not a critical requirement.
Marine Stainless Steel Wood Screws
When it comes to marine applications involving wooden structures—be it decking, handrails, or cabinetry—the choice of fasteners is as critical as the choice of wood itself. One material that consistently stands out as the ideal fastener for wooden fixtures and fittings in marine environments is marine stainless steel wood screws. These fasteners provide a perfect blend of aesthetic sophistication and robust performance, fulfilling both visual and functional requirements with unparalleled effectiveness.
Aesthetic Appeal
Starting with the visual aspect, marine stainless steel wood screws offer a clean, sleek look that naturally complements the rich textures of wooden structures. Unlike other types of screws, which may clash visually with wood or rust over time, thereby tarnishing the appearance, marine stainless steel screws maintain their polished appearance. This enduring aesthetic appeal makes them an attractive choice for luxury boats, yachts, and high-end marine installations, where every detail matters.
Robust Performance
On the performance front, marine stainless steel wood screws are engineered to meet the rigorous demands of the marine environment. The unique blend of elements in the stainless steel alloy, often featuring increased levels of chromium and nickel, offers superior corrosion resistance. This is crucial in marine settings, where screws are often exposed to corrosive saltwater and fluctuating weather conditions. The anti-corrosive properties of marine stainless steel wood screws ensure that they do not weaken or break down over time, thereby ensuring the longevity of the wooden structures they secure.
Versatility in Applications
Besides decking, these screws are incredibly versatile and are utilized in a variety of applications. From securing wooden paneling inside a ship’s cabin to fastening handrails on a pier, marine stainless steel wood screws can handle a wide range of tasks. Their exceptional holding power ensures that wooden pieces are firmly joined, providing a robust and stable structure capable of enduring the daily rigors of marine life.
Ease of Installation
Moreover, many marine stainless steel wood screws come equipped with features that facilitate easy installation. Whether it’s a self-tapping tip that eliminates the need for pre-drilling or a countersunk head that allows for a flush finish, these design features simplify the installation process, saving both time and labor costs.
Long-term Cost-Effectiveness
It’s also worth noting that while marine stainless steel wood screws may come with a higher upfront cost compared to other types of screws, their durability and low maintenance requirements often translate to long-term savings. When you consider the costs associated with replacing or repairing corroded or damaged screws, the long-term cost-effectiveness of marine stainless steel wood screws becomes abundantly clear.
In summary, marine stainless steel wood screws are more than just fasteners; they are a vital component that ensures the functional integrity and aesthetic appeal of wooden structures in marine settings. By offering a high degree of corrosion resistance, superb holding power, and a visually pleasing finish, these screws have established themselves as the go-to choice for professionals in the marine construction industry.
Black Marine Screws and Marine Screw Covers
In the intricate world of marine fasteners, the confluence of functionality and aesthetic appeal is becoming an increasingly important consideration. A compelling example of this trend is the growing popularity of black marine screws and marine screw covers. Far from being mere ornamental additions, these components serve to elevate both the visual and functional aspects of various marine structures, offering a blend of practicality and design sophistication that’s hard to overlook.
The Allure of Black Marine Screws
Black marine screws are not just your ordinary fasteners given a dark hue; they’re meticulously engineered to provide the best of both worlds. Crafted from materials that offer robust performance and corrosion resistance—attributes essential for any marine setting—these screws are coated with specialized finishes like black oxide or black zinc. These coatings not only enhance the aesthetic appeal but also add an extra layer of protection against corrosive elements commonly found in marine environments.
The dark, sleek look of black marine screws can be a perfect complement to modern design themes, adding a touch of elegance and contrast to wooden or metallic structures. Whether it’s a contemporary yacht interior or a stylish dockside restaurant, the subtle elegance of black marine screws offers a visually pleasing counterpoint to traditional stainless steel or brass options.
The Functionality of Marine Screw Covers
On the other end of the aesthetic spectrum, marine screw covers provide a seamless look by concealing the heads of screws. Made from various materials such as plastic, stainless steel, or even specialized rubber, these covers offer an additional layer of protection to the screw head, shielding it from direct exposure to corrosive elements. This added protection contributes to the overall durability and longevity of the fastening system.
Stylistic Integration and Versatility
What makes these black screws and screw covers particularly appealing is how effortlessly they can be integrated into various designs. Whether the overarching aesthetic calls for a sleek, modern appearance or a more rustic, natural look, these components adapt seamlessly. In this sense, their design versatility makes them a popular choice for boat builders, marine architects, and even DIY enthusiasts looking to add a touch of sophistication to their marine projects.
Longevity and Durability
It’s essential to note that the growing popularity of black marine screws and marine screw covers isn’t just a design fad; it’s an acknowledgment of the need for fasteners that offer both durability and aesthetic appeal. By selecting these stylish yet functional components, one can ensure a longer lifespan for marine structures, making them a cost-effective choice in the long run.
In conclusion, the increasing popularity of black marine screws and marine screw covers signifies a broader trend in the marine industry—acknowledging the importance of aesthetic considerations without compromising on functionality. These components offer an elegant solution to the age-old challenge of blending form and function, making them a go-to choice for those looking to achieve both structural integrity and design excellence in marine environments.
Specialty Marine Fasteners
In the realm of marine construction and maintenance, specialty marine fasteners occupy a crucial role that transcends the capabilities of standard screws and bolts. These are not just mere fasteners; they are highly engineered components designed to meet the unique challenges posed by the marine environment—corrosive saltwater, fluctuating temperatures, and high-pressure conditions, to name a few. Typically made from high-grade materials like 316 stainless steel, bronze, or even specialized plastics, these fasteners come in a variety of designs and coatings to offer unparalleled corrosion resistance and mechanical strength. Whether it’s securing a ship’s hull, stabilizing offshore drilling platforms, or ensuring the durability of marine furniture and fixtures, specialty marine fasteners are the unsung heroes that provide an essential blend of reliability and performance. Their versatility makes them ideal for a multitude of applications, extending their utility beyond just structural integrity to include specialized functions like vibration damping, electrical conductivity, or even aesthetic considerations.
Marine Clips Fasteners and Marine Panel Fasteners
In marine construction and maintenance, the need for specialized fastening solutions extends beyond the realm of screws and bolts. Among the often-overlooked yet critical components in this category are marine clips fasteners and marine panel fasteners. Designed with a specific function in mind—namely, securing panels and clips in place—these fasteners are an integral part of many marine structures and assemblies.
Durability and Corrosion Resistance
Similar to other fasteners that are intended for marine applications, marine clips fasteners and marine panel fasteners must meet stringent criteria for corrosion resistance. Often constructed from materials like stainless steel, aluminum, or corrosion-resistant alloys, these fasteners are engineered to withstand the harshest of marine conditions. Their corrosion-resistant attributes make them exceptionally well-suited for areas that are regularly exposed to the abrasive elements of saltwater, humidity, and varying temperatures.
Specialized Design for Panel and Clip Attachment
What sets these fasteners apart is their specialized design tailored for attaching panels and clips securely. This is particularly important in marine settings, where the constant motion of the water and the structure can exert significant force on these elements. Failure to secure panels and clips adequately can result in the compromise of an entire assembly, highlighting the vital role these fasteners play. Depending on the specific application, marine clips fasteners and marine panel fasteners may come with unique features such as self-locking mechanisms or vibration-resistant designs to ensure optimal performance.
Versatile Applications
Their specialized focus notwithstanding, marine clips fasteners and marine panel fasteners offer versatile applications. They are commonly used in a range of settings from boat interiors, marine furniture, and cabin assemblies to larger constructs like marinas and offshore platforms. The specific choice of fastener often depends on the material of the panels or clips to be attached, their weight, and the environmental conditions they will be exposed to, allowing for a customizable approach to meet various needs.
Long-term Reliability
When it comes to long-term performance and reliability, opting for specialized marine clips fasteners and marine panel fasteners is a wise investment. Their corrosion-resistant properties significantly extend the lifespan of the panels and clips they secure, ultimately contributing to the overall durability and longevity of the marine structure they are part of.
In summary, marine clips fasteners and marine panel fasteners serve as specialized, effective solutions for the challenges of panel and clip attachment in marine environments. Through their durability, specialized design, and versatility, they stand as a testament to the importance of choosing the right fastener for the right application in marine construction and maintenance.
Marine Blind Hole Fasteners and Marine Fastener Kit
When it comes to marine applications, the requirements for fastening solutions often go beyond the usual specifications. Two notable examples that address very specific needs are marine blind hole fasteners and marine fastener kits. Both of these components serve specialized functions, ensuring that even the most complex marine installations can maintain their integrity in the harsh environments they operate in.
The Importance of Marine Blind Hole Fasteners
Marine blind hole fasteners stand out for their specialized application: they are specifically designed for situations where access to the opposite side of the material is either limited or entirely unavailable. This makes them indispensable for marine engineers and craftsmen who often find themselves working in constrained spaces like ship interiors, underwater structures, or tight engine compartments. The ability to securely fasten materials from one side not only simplifies the installation process but also ensures a secure, long-lasting connection that can withstand the extreme conditions typical of marine environments. Often made from corrosion-resistant materials such as marine-grade stainless steel or specialized alloys, these fasteners offer durability while fulfilling their specialized role effectively.
The Versatility of Marine Fastener Kits
On the other hand, marine fastener kits serve as an all-in-one solution for a variety of marine applications. These kits are generally designed to provide a comprehensive set of fasteners that one may need for any number of marine-related tasks, from regular maintenance and minor repairs to complete overhauls or new builds. A standard marine fastener kit may include various types of screws, bolts, washers, and other essential fasteners, all meticulously selected to meet the corrosion-resistant criteria necessary for long-term exposure to saltwater and other corrosive elements. These kits are an invaluable resource, particularly for individuals who frequently engage in marine projects, offering the convenience of having a wide array of specialized fasteners readily available.
Combining Functionality with Practicality
Both marine blind hole fasteners and marine fastener kits epitomize the combination of functionality and practicality. While the blind hole fasteners resolve the specific problem of single-sided access, marine fastener kits offer a broad spectrum of fastening solutions, ensuring you’re well-equipped for almost any marine challenge that may arise. Having a dedicated kit on hand simplifies the logistics, allowing you to focus more on the task at hand and less on sourcing individual components. It also offers the peace of mind that comes with knowing that the fasteners you’re using are engineered to meet the rigorous demands of marine environments.
In summary, marine blind hole fasteners and marine fastener kits offer specialized, effective solutions for the unique challenges posed by marine applications. The specialized design of blind hole fasteners addresses issues of accessibility, while the comprehensive nature of marine fastener kits provides an all-in-one solution for multiple needs. By investing in these specialized fastening solutions, you are taking a significant step toward ensuring the long-term integrity and durability of your marine projects.
Marine Screw Anchor and Screw Marine Anchors
When it comes to maritime safety and structural integrity, one component that demands particular attention is the marine screw anchor. Also known as screw marine anchors, these specialized fastening devices are indispensable for securing boats, ships, and offshore platforms. Given the extreme conditions of marine environments—oscillating between tempestuous seas and corrosive saltwater—marine screw anchors must meet rigorous standards of durability and reliability.
The Role of Marine Screw Anchors
Marine screw anchors are designed to serve a very specific yet critical function: they provide stable anchorage points in underwater or maritime settings where traditional anchoring methods might not be effective or possible. By being driven into the sea bed or other substrates, these anchors offer secure fastening that can withstand both the dynamic and static loads often encountered at sea, including strong currents, winds, and tidal forces. This level of stability is particularly crucial for larger maritime structures like offshore drilling platforms, where the safety of many lives and significant investments may depend on the reliability of such anchoring systems.
Material Considerations and Durability
Constructed usually from marine-grade stainless steel, aluminum, or specialized marine alloys, marine screw anchors offer exceptional resistance to the corrosive forces of saltwater. These materials are meticulously selected not just for their ability to resist corrosion but also for their mechanical strength, ensuring that the anchors can bear the significant forces to which they will be subjected. The result is a component that fulfills its function effectively while also being long-lasting, which is an essential trait given the critical role these anchors play in marine safety.
Adaptability and Versatility
Despite their specialized role, marine screw anchors are remarkably adaptable and can be used in various configurations and settings. Whether it’s a small recreational boat, a fishing vessel, or a colossal offshore oil rig, there is usually a marine screw anchor designed to meet that specific need. Their designs may also include features like flukes, spiral threads, or other innovative elements that enhance their holding power, ensuring that they can adapt to various seabed compositions from sandy and muddy to rocky.
Ensuring Long-term Safety
The importance of choosing the right marine screw anchor cannot be overstated. Given their role in securing not just structures but also lives and valuable resources, opting for high-quality, marine-grade screw anchors is a non-negotiable requirement. Proper installation and regular inspections are equally critical to ensure that these anchors continue to perform their essential function over time.
In summary, marine screw anchors, or screw marine anchors, are specialized but crucial components in maritime operations that require the highest standards of quality, durability, and performance. Through their specialized design, material quality, and adaptable features, these anchors serve as the bedrock of maritime safety and structural stability, making them an indispensable asset in any serious marine endeavor.
Self Tapping Marine Screws
In the world of marine construction and repair, efficiency and durability are two characteristics that are often sought but rarely found in a single component. This is where self-tapping marine screws come into the picture. These ingenious fasteners are specifically designed to streamline the installation process while offering the structural integrity that is absolutely crucial for any marine application.
The Unique Features of Self-Tapping Marine Screws
What sets self-tapping marine screws apart is their ability to form their own threads or “tap” their own holes as they are being driven into the material. This eliminates the need for pre-drilling holes, a step that is usually required when using traditional screws. The self-tapping feature is made possible by the screw’s unique design, which includes a tapered tip and specialized threading that can cut through materials, thereby creating a snug and secure fit as it is installed.
Advantages in Time and Labor
The time-saving aspect of self-tapping marine screws is one of their most significant advantages. In the fast-paced world of marine construction and maintenance, time is often of the essence. The ability to forego pre-drilling steps and move directly to installation accelerates project timelines, allowing for quicker completion and less downtime. This is particularly beneficial in large-scale projects or emergency repair situations where any delay can result in substantial financial or safety repercussions.
Material Compatibility and Durability
Typically made from marine-grade materials like 316 stainless steel, self-tapping marine screws are built to last. Their corrosion resistance makes them ideal for long-term exposure to saltwater and other harsh elements typical of marine environments. This is not just an advantage in terms of durability; it’s a safety feature that ensures that once these screws are installed, they will maintain their structural integrity even under the most demanding conditions.
Versatility Across Applications
Self-tapping marine screws are not just limited to a single type of application; their versatility makes them ideal for a range of uses, from securing decking and hull components to fastening accessories and equipment onboard. Their self-tapping capability means they can be used on various materials like wood, metal, and even some plastics, making them a multi-purpose fastener that is as versatile as it is durable.
Conclusion: An Invaluable Asset in Marine Construction
In summary, self-tapping marine screws are more than just fasteners; they are invaluable tools designed to make marine construction and repair more efficient, reliable, and durable. Their unique self-tapping feature streamlines the installation process, their material composition ensures longevity, and their versatility makes them adaptable for a wide range of applications. Any marine project aiming for a balance of speed, strength, and reliability should seriously consider the inclusion of self-tapping marine screws as part of their fastening arsenal.
You may also want to read about aerospace screws, what are fasteners, and the best wood screws.
Considerations for Selecting the Best Screws for Marine Use
When embarking on any marine-related construction or repair project, the choice of fasteners is not something to be taken lightly. Various factors come into play, each requiring careful consideration to ensure not just optimal performance but also long-term durability. Material is often the first aspect to examine; marine-grade stainless steel, brass, and bronze are popular choices for their anti-corrosive properties. However, it’s also essential to consider the specific application needs. For instance, if the screws will bear heavy loads, you’ll want options with high tensile strength. The environment is another critical aspect; screws exposed to extreme conditions such as fluctuating temperatures or corrosive saltwater need to be exceptionally resilient. Additional features like self-tapping capability, specialized threading, and coating can further optimize the fastener for its intended application. It’s not just a matter of selecting a marine-grade screw and calling it a day; it’s about understanding the nuances of your project and choosing a fastener that aligns perfectly with those specific needs.
Marine Grade Stainless Steel Wood Screws and Marine Grade Self Tapping Screws
When it comes to marine construction and repair involving wooden elements—be it decking, furniture, or structural components—marine-grade stainless steel wood screws offer an unmatched blend of strength and corrosion resistance. Crafted to withstand the harshest marine environments, these screws not only provide exceptional holding power but also maintain their integrity despite continuous exposure to saltwater and varying weather conditions.
Similarly, for projects that require a streamlined installation process without compromising durability, marine-grade self-tapping screws are the go-to solution. These specialized fasteners have the capability to create their own threads as they are driven into material, eliminating the need for pre-drilled holes and saving valuable time and effort. They are most often made of marine-grade materials such as 316 stainless steel, ensuring that they are up to the task in terms of both longevity and performance.
The bottom line is, whether you’re working with wood or looking for self-tapping efficiency, opting for marine-grade fasteners is non-negotiable. Given the harsh conditions these components will face, settling for anything less would be a compromise that could lead to premature wear, component failure, and, ultimately, increased costs in terms of repairs and replacements.
Marine Quality Stainless Steel Screws
When it comes to choosing the right screws for marine applications, not just any stainless steel variant will suffice. The phrase “marine quality” carries significant weight, signaling that the screws meet or exceed stringent standards tailored for the harsh realities of marine environments. One commonly referenced set of guidelines are the AISI (American Iron and Steel Institute) standards, which serve as an industry benchmark for the quality and performance of stainless steel products.
Adhering to these standards ensures that the marine quality stainless steel screws you choose will possess the essential properties for withstanding corrosion, extreme temperatures, and mechanical stresses. This level of assurance is invaluable, especially for applications that will be continuously exposed to the rigors of saltwater, UV rays, and changing weather conditions.
It’s not just about choosing a stainless steel screw that looks durable; it’s about making an informed decision based on internationally recognized quality standards. This attention to detail is crucial, as failing to adhere to these standards could result in compromised structural integrity, more frequent maintenance, and ultimately, greater long-term costs. When the safety and durability of marine structures are at stake, ensuring your fasteners meet the requisite quality standards like the AISI is an investment in peace of mind and project success.
Marine Stainless Steel Screws 316
For marine applications that entail consistent or severe exposure to corrosive elements like saltwater, the quality of the stainless steel used in your screws can make a significant difference in both durability and safety. In scenarios like these, 316-grade stainless steel screws are often the most advisable choice. This specific grade includes the element molybdenum, an addition that dramatically enhances the material’s resistance to chlorides and other corrosive substances commonly found in marine settings.
But what makes 316-grade stand out isn’t just its ability to resist corrosion. Its mechanical properties, including tensile strength and yield strength, make it ideal for applications where structural integrity is paramount. These screws are often used in critical structural components of boats, piers, and offshore platforms where failure isn’t an option.
The choice of 316-grade stainless steel screws is also aligned with best practices and recommendations from industry bodies and engineering consultants. While they may come at a slightly higher initial cost compared to other grades, the long-term savings in maintenance, replacements, and potential liabilities make them a prudent investment for any serious marine application.
Choosing 316-grade stainless steel screws is not just an option; it’s often a necessity when the risks associated with corrosion, stress, and environmental factors are high. Thus, making the informed decision to opt for 316-grade stainless steel screws can pay dividends in terms of both durability and peace of mind.
While the focus is often on the primary fastening components like screws and bolts, one must not overlook the importance of accessories such as screw caps and covers, especially in marine applications. These seemingly minor elements play a vital role in not only concealing screw heads for a more polished appearance but also adding an extra layer of protection against environmental factors. Therefore, just like the primary fasteners, these accessories should also meet marine-grade specifications.
Opting for marine-grade screw caps and covers ensures that these accessories possess the same high level of corrosion resistance as the screws themselves. Manufactured from materials like 316-grade stainless steel or marine-grade plastics, they offer an additional barrier against the corrosive power of saltwater, harsh chemicals, and extreme weather conditions.
It’s not merely a cosmetic choice. By using marine-grade caps and covers, you contribute to the overall structural integrity and lifespan of the marine application, whether it’s a boat, a dock, or an offshore drilling platform. These caps and covers are designed to withstand the same rigorous conditions as marine screws and offer the benefit of reducing maintenance needs over time.
In summary, the integrity of your marine construction doesn’t end with selecting the right screws; it extends to all elements of the fastening system, including caps and covers. Neglecting to use marine-grade accessories could lead to the premature degradation of the fastener assembly, ultimately compromising safety and increasing long-term costs. Therefore, when aiming for a resilient marine application, choosing marine-grade screw caps and covers is just as crucial.
In conclusion, the role that marine screws and fasteners play in maritime applications cannot be overstated. They are the linchpins that hold together intricate structures, whether it’s a luxury yacht, an industrial offshore platform, or a simple dock. Making the right material selection is not just a box to tick; it’s a critical decision that will have far-reaching consequences for the lifespan, safety, and overall reliability of your maritime structures.
From stainless marine screws that offer unparalleled corrosion resistance to marine bronze fasteners that provide natural resilience against environmental factors, each type of fastener comes with its own set of advantages and limitations. Then there are specialized options like marine-grade stainless steel wood screws, designed to deliver robust performance in wood applications without sacrificing aesthetic appeal.
Compromising on quality is not just ill-advised; it’s a risk that could lead to structural failures, increased maintenance costs, and, in the worst cases, catastrophic events. Therefore, due diligence is imperative. This involves understanding the specific demands of your marine application, consulting with engineering experts, and adhering to industry standards and guidelines.
Furthermore, the fastener selection process also extends to the accessories, like caps and covers, which should also meet marine-grade criteria. After all, a chain is only as strong as its weakest link, and in the world of marine applications, every component plays a vital role.
In a setting where the elements are unforgiving and the margin for error is minimal, the importance of making informed choices for your marine screws and fasteners cannot be emphasized enough. By prioritizing quality, durability, and suitability for the specific challenges of saltwater environments, you’re investing in a solution designed to stand the test of time.
No Comments