In today’s fast-paced industrial era, the importance of screws and fasteners cannot be overstated. They are the building blocks that hold everything together—from the tiny components in your smartphone to the towering skyscrapers in your city. This article aims to provide an in-depth understanding of the manufacturing processes involved in creating screws and fasteners. This screw and fastener manufacturing guide is crucial for anyone in the screw manufacturing industry, fastener manufacturing companies, and even specialty screw manufacturing.
Table of Contents
Types of Screw and Fastener Manufacturing
Before diving deep into the manufacturing process, it’s crucial to understand the variety of screws and fasteners that are produced. From micro screw manufacturing to self-drilling screws, there are various types with unique requirements and manufacturing techniques.
- Precision Screw Manufacturing: Primarily used in sensitive machinery like aerospace or medical devices.
- Micro Screw Manufacturing: These are microscopic screws often used in gadgets and electronics.
- Self Drilling Screw Manufacturing: These screws can drill their own holes during installation.
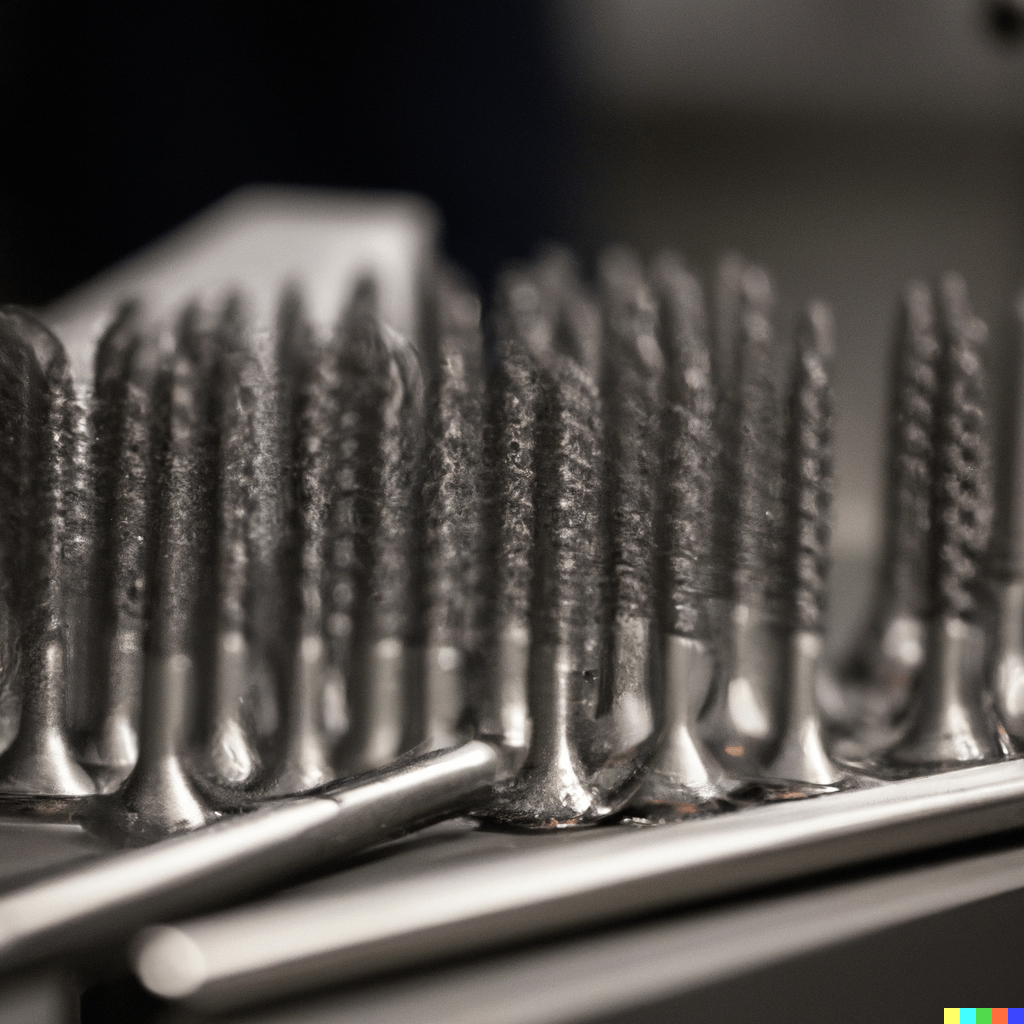
Key Machinery in Screw Manufacturing
- Screw Manufacturing Machine: The heart of the operation, responsible for the forming and threading of screws.
- Fastener Manufacturing Machine: This machine performs operations like cold forging, head forming, and threading for fasteners.
- Drywall Screw Manufacturing Machine: Specially designed machines for creating drywall screws.
Key Machinery in Screw Manufacturing: An In-depth Examination
In the realm of screw and fastener manufacturing, the machinery deployed is often specialized to cater to the diverse range of products. These machines not only form the backbone of the production process but also are the workhorses that ensure scalability, quality, and precision. Here are some key pieces of equipment commonly found in screw manufacturing facilities:
Screw Manufacturing Machine
Often referred to as the heart of the operation, the screw manufacturing machine is a marvel of mechanical engineering. It is responsible for the most vital processes such as forming and threading of screws. Essentially, these machines take in raw material—usually in the form of metal rods—and transform it into screws through a series of steps that may include cutting, heading, and threading.
- Forming: The machine utilizes dies and punches to form the head and body of the screw.
- Threading: Through a process known as thread rolling, threads are added onto the screw’s body. High-precision thread rolling machines ensure that the threads meet the necessary specifications and tolerances.
- Price Considerations: When it comes to the screw manufacturing machine price list, the costs can range significantly based on functionality, speed, and brand.
Fastener Manufacturing Machine
Another critical piece of machinery is the fastener manufacturing machine, which is tailored for making various types of fasteners, from nuts and bolts to washers. These machines perform multiple operations like cold forging, head forming, and threading.
- Cold Forging: The machine applies pressure to shape the metal into the desired fastener form, generally at room temperature, which enhances the metal’s mechanical properties.
- Head Forming: Special dies are used to form the heads of bolts or screws, ensuring they meet dimensional requirements.
- Threading: Similar to screw manufacturing machines, these machines also add threads but usually at a larger scale and sometimes with varied thread forms to suit different fasteners.
Drywall Screw Manufacturing Machine
Drywall screws are specialized screws designed to fasten drywall to wood or metal surfaces, and as such, they require their own specialized manufacturing machines. These machines are engineered to produce screws that are both sharp and strong, with threads optimized for the best holding power in drywall applications.
- Material Handling: These machines often work with different material compositions to create screws with the ideal balance of strength and ductility.
- Thread Design: Given that drywall screws need to penetrate and grip effectively, the threading process for these screws is especially critical.
Understanding the role, function, and technical capabilities of these machines offers a glimpse into the complex world of screw manufacturing. Whether you are sourcing machinery or simply seeking to understand the production process, recognizing the capabilities of these machines is crucial.
Screw Manufacturing Machine Price List
While it’s difficult to provide an exhaustive price list, quality machines can range approximately from $5,000 to $100,000 depending on their functionality and brand.
The Screw Manufacturing Process
To give a clear insight, here’s a simplified screw manufacturing process flow chart:
- Material Selection: Usually stainless steel, aluminum, or alloy.
- Cold Forging: Initial shaping of the material.
- Thread Cutting: Employing a screw thread manufacturing process.
- Heat Treatment: For increased durability.
- Plating: For resistance against corrosion.
The Screw Manufacturing Process: A Detailed Walkthrough
The manufacturing process for screws is a fascinating amalgamation of materials science, mechanical engineering, and industrial precision. To understand it fully, it’s essential to look at each step in detail. Below is an expanded explanation of the screw manufacturing process, based on a simplified flow chart.
Material Selection
The initial step in the process involves selecting the appropriate material for the screws. Common choices include stainless steel, aluminum, or alloy metals. The choice of material is dependent on the application and the conditions under which the screw will operate. For example, stainless steel is often selected for its corrosion resistance, while aluminum might be chosen for its lightweight properties.
Cold Forging
Once the material is selected, it is shaped into screws using a process known as cold forging. Cold forging is performed at or near room temperature and involves shaping the material using localized compressive forces. The benefit of cold forging over hot forging is that it offers better dimensional control, superior surface finish, and enhanced mechanical properties. During this stage, the basic shape of the screw, including its head and body, is formed.
Thread Cutting
The next critical step is thread cutting, a part of the screw thread manufacturing process. This is usually achieved through thread rolling or cutting processes, where the screw is passed between two rolling dies to carve out the threads. The accuracy of thread cutting is vital for the screw’s functionality; poorly cut threads can result in a screw that is either too loose or too difficult to insert.
Heat Treatment
After forming and threading, screws often undergo a heat treatment process to enhance their mechanical properties. This involves heating the screws to a specific temperature and then cooling them at a controlled rate. The process increases the durability, toughness, and hardness of the screws, making them more resistant to wear and tear.
Plating
The final stage is plating, which is crucial for enhancing the screw’s resistance against corrosion and environmental degradation. Various plating techniques can be employed, including zinc, nickel, or chrome plating. The choice of plating material is usually determined by the screw’s intended application and the specific corrosion-resistance requirements.
By understanding the ins and outs of each phase in the screw manufacturing process, one can gain a better appreciation for the engineering prowess that goes into creating these small but indispensable fasteners. Whether you are in the screw manufacturing business or merely curious about industrial processes, this information offers a foundational understanding of how screws are made from start to finish.
Fastener Manufacturing: An Overview
Fasteners, unlike screws, are generally manufactured using high-speed machines that can perform multiple operations, including drilling, threading, and quality control. Fastener manufacturing companies often use specialized fastener manufacturing equipment for bulk production.
Specialty Screw Manufacturing
Specialty screws like self-drilling screws undergo a slightly different manufacturing process that involves specialized drill tips and higher quality materials.
Specialty Screw Manufacturing: A Closer Look
When it comes to the world of screws and fasteners, ‘specialty’ is a term that often encapsulates products designed for very specific applications or industries. Among these specialty screws, self-drilling screws stand out due to their unique manufacturing process and functionality. Unlike standard screws, self-drilling screws are engineered to serve a dual purpose: they not only fasten materials together but also drill their own holes, eliminating the need for a pre-drilled hole.
Specialized Drill Tips
The magic lies in the specialized drill tips that these screws possess. These drill tips are typically made from high-speed steel or carbides, designed to effortlessly penetrate through materials such as metal, wood, or plastic. This eliminates the need for a separate drilling process, thus saving time and reducing labor costs. To manufacture these drill tips, precision engineering is paramount. They are often shaped and sharpened using specialized CNC machines to ensure maximum efficacy.
Higher Quality Materials
Specialty screws also demand higher quality materials to ensure they meet the required performance standards. For instance, materials like stainless steel, high-grade aluminum, or titanium are frequently used in the manufacture of specialty screws. These materials offer attributes like corrosion resistance, higher tensile strength, and durability, which are often crucial for applications that these screws are used for.
Advanced Coating Techniques
Moreover, these screws often undergo advanced coating processes, such as PTFE or Zinc plating, to further enhance their corrosion resistance and reduce friction during the drilling process. Such coatings not only prolong the lifespan of the screws but also make the installation process smoother.
Quality Control
Given the specialized nature of these screws, quality control is even more stringent. This often involves advanced inspection techniques, such as X-ray fluorescence for material composition analysis and digital microscopy for scrutinizing the thread geometry.
By understanding the intricacies involved in the manufacturing of specialty screws like self-drilling screws, you can appreciate the advanced engineering and attention to detail that goes into their production. It’s this meticulous craftsmanship that sets them apart, making them a preferred choice for various industrial applications.
Quality Assurance in Screw and Fastener Manufacturing
Quality assurance is paramount in the screw and fastener manufacturing industry. This is where companies differentiate themselves to become the best fastener manufacturing company or set screw manufacturing company in the market.
- Precision Testing: Ensures the screws and fasteners meet exact specifications.
- Corrosion Resistance: Tested for durability and longevity.
Screw Manufacturing Industry Trends
- Automation: Reducing manual labor and errors.
- Sustainability: Eco-friendly processes and materials.
Understanding the complex world of screw and fastener manufacturing is crucial for any industry professional, whether you’re looking for a fastener manufacturing factory, interested in the nut bolt screw manufacturing industry, or exploring fastener specialties manufacturing.
You may want to read also about how to measure screw size.
By focusing on quality and innovation, companies can set themselves apart in the fastener manufacturing industry, achieving remarkable outcomes that drive the industry forward.
No Comments